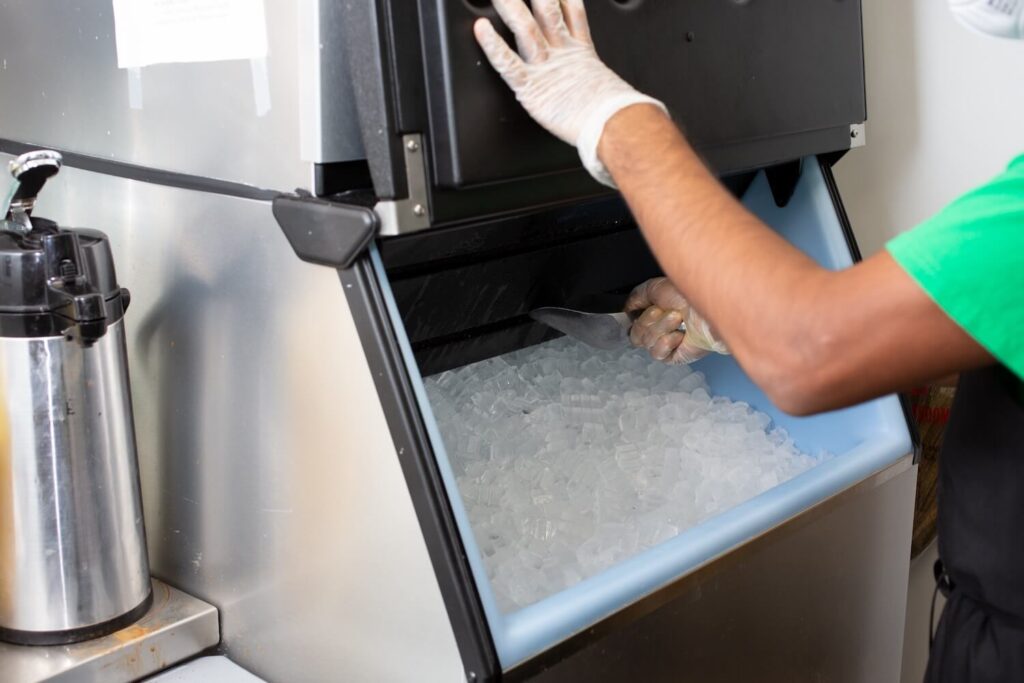
In the bustling world of business, especially in industries like hospitality, food service, healthcare, and retail, ice machines are often overlooked heroes. These essential pieces of equipment work tirelessly in the background, providing the foundation for smooth operations, excellent customer service, and adherence to health standards. However, the moment an ice machine malfunctions, its absence becomes glaringly obvious. Drinks warm up, perishables lose their cooling buffer, and customer satisfaction begins to falter.
Timely ice machine repair and maintenance isn’t just a matter of convenience—it’s a critical factor that can impact your business’s bottom line, reputation, and daily operations.
This article dives into the significant role ice machines play, the consequences of ignoring their upkeep, and how businesses can prevent disruptions by prioritizing regular repairs.
1. The Hidden Backbone of Business: Ice Machines Across Industries
To appreciate the importance of ice machine repair, it’s vital to understand how deeply embedded these machines are in various industries. Whether it’s a small café or a sprawling hospital, ice machines serve purposes that are integral to operations.
Food and Beverage Industry
In restaurants, bars, and coffee shops, ice isn’t just an accessory—it’s an expectation. Customers rely on ice to enjoy chilled beverages, and chefs need it for food preparation and preservation. Without it, service slows, food safety is jeopardized, and customers leave disappointed.
For example, imagine a bar during a hot summer evening running out of ice mid-shift. Cocktails can’t be served as intended, leading to frustrated patrons and lost revenue. Even a temporary workaround, like purchasing bagged ice, increases costs and disrupts workflows.
Hotels and Hospitality
In the hospitality industry, guest satisfaction is paramount. Ice machines, often stationed conveniently on hotel floors, are considered a hallmark of good service. Guests use ice for drinks, medical needs, and even food storage during their stays. A broken ice machine can result in frustrated guests and negative reviews that harm your reputation.
Healthcare and Medical Facilities
Hospitals and clinics use ice for a variety of purposes, from therapeutic treatments like ice packs for injuries to storing medications that require a cool environment. A malfunctioning ice machine in a medical facility isn’t just inconvenient—it can directly impact patient care and safety.
Retail and Grocery Stores
Ice isn’t just for beverages; it’s critical for food presentation. Fresh seafood, meats, and other perishables are displayed on ice to ensure they remain fresh and visually appealing. A broken ice machine could lead to spoilage, inventory loss, and even health violations.
Catering and Event Management
Catering companies and event planners rely on ice for large gatherings where drinks need to stay cold, and food must remain fresh. A failure here can ruin an event’s success and tarnish the reputation of the service provider.
2. The Domino Effect: Consequences of Ice Machine Breakdowns
An ice machine failure isn’t an isolated incident—it triggers a chain reaction that can disrupt multiple When an ice machine breaks down, the ramifications are far-reaching, often creating a ripple effect that disrupts multiple aspects of your business. While the immediate impact may seem minor, the cumulative consequences can significantly affect your operations, finances, and reputation. Here’s a detailed look at how a single malfunction can snowball into larger problems:
Operational Disruptions
When an ice machine fails, businesses scramble to find alternatives. Staff may have to purchase and transport bagged ice, which takes time, disrupts workflows, and adds to labor costs.
Financial Impact
The costs of ignoring timely repairs extend beyond the price of fixing the machine. Consider the lost revenue from unsatisfied customers, the expense of temporary fixes like bagged ice, and potential fines for failing to meet health code regulations.
Customer Dissatisfaction
In service-oriented industries, customer expectations are high. Whether it’s a warm drink or unappealing food presentation, even small inconveniences can result in negative online reviews. In the digital age, such reviews can have a long-term impact on a business’s reputation and ability to attract new customers.
Health and Safety Risks
Ice is classified as food by health authorities, and contamination poses serious risks. A malfunctioning or poorly maintained machine may produce ice with bacterial contamination, leading to potential health code violations and legal repercussions.
3. Common Issues in Ice Machines and Their Warning Signs
Ice machines are complex pieces of equipment with several moving parts and systems that must work together seamlessly. When any one component falters, it can lead to noticeable issues. Identifying these problems early can save your business from costly repairs, operational disruptions, and potential health risks. Below are the most common ice machine issues, their warning signs, and what they might indicate.
Reduced Ice Production
A noticeable decline in ice output may be due to clogged filters, insufficient water flow, or mechanical malfunctions.
Contaminated or Poor-Quality Ice
Cloudy, dirty, or foul-tasting ice is often a sign of mineral buildup, mold, or a dirty water supply. This can affect customer satisfaction and pose health risks.
Water Leaks
Leaking water around the machine could point to loose connections, cracked hoses, or a clogged drainage system.
Unusual Noises
Grinding, buzzing, or rattling sounds often indicate worn-out internal components that require immediate attention.
Overheating or Inconsistent Temperatures
If the machine runs too hot or struggles to maintain a consistent freezing temperature, it can lead to incomplete or malformed ice.
4. Why Timely Repairs Are Non-Negotiable
Delaying ice machine repairs may seem like a way to save money in the short term, but it often results in far greater costs, disruptions, and stress in the long run. Ice machines are complex pieces of equipment with interconnected systems, and when one component begins to fail, it can quickly cascade into larger issues. Here are several reasons why timely repairs are essential for your business.
Prevent Escalating Damage
What starts as a minor issue, such as a clogged filter, can evolve into major problems like a damaged compressor. Addressing repairs early saves money in the long run.
Maintain Equipment Lifespan
Regular maintenance and prompt repairs extend the life of your ice machine, delaying the need for costly replacements.
Reduce Utility Costs
A malfunctioning machine often consumes more energy and water, inflating utility bills unnecessarily.
Avoid Business Downtime
Proactive repair minimizes the risk of unexpected breakdowns during critical business hours, ensuring uninterrupted service.
5. The Value of Professional Repair Services
When your ice machine malfunctions, the temptation to save money by attempting a DIY repair or relying on unqualified technicians can be strong. However, the long-term benefits of hiring professional repair services far outweigh the short-term cost savings. Working with professionals ensures that your ice machine is restored to optimal performance quickly, safely, and efficiently, minimizing disruptions to your business.
Expertise and Experience
Certified technicians are trained to diagnose and resolve issues efficiently, saving time and preventing misdiagnoses.
Warranty Protection
Most machines come with warranties that require repairs by authorized professionals. Attempting DIY repairs could void this coverage.
Access to Quality Parts
Professionals use genuine parts that match the specifications of your machine, ensuring a long-lasting repair.
6. How Preventive Maintenance Reduces Breakdowns
Preventive maintenance is the unsung hero of keeping your ice machine in top condition. While repairs address existing issues, maintenance works proactively to prevent problems before they arise. Investing time and resources into a regular maintenance schedule can save businesses thousands of dollars in repair costs, minimize operational disruptions, and extend the lifespan of the equipment.
Benefits of Regular Maintenance
- Improved Performance: Over time, ice machines accumulate scale, dirt, and mineral deposits that hinder their ability to produce ice efficiently. Preventive maintenance ensures that critical components, such as the evaporator, condenser, and water lines, are cleaned and inspected regularly. This upkeep not only boosts ice production but also maintains the quality and clarity of the ice, which is especially important in customer-facing industries.
- Extended Lifespan: An ice machine is a significant investment, and replacing one prematurely can be costly. Preventive maintenance helps your machine run smoothly for years, delaying the need for replacement. By addressing wear and tear early—such as tightening loose connections or replacing worn-out parts—you can significantly increase your equipment’s operational lifespan.
- Compliance with Health Standards: Health codes classify ice as a food item, which means the production and storage of ice must meet strict sanitation standards. Regular maintenance includes cleaning and sanitizing internal components, reducing the risk of bacteria or mold contamination. This ensures that your business stays compliant with health regulations and protects customers from potential health risks.
- Lower Repair Costs: Small problems, if ignored, can escalate into larger, more expensive repairs. For example, a clogged water filter can strain the compressor, leading to a complete system failure. Preventive maintenance identifies and resolves such issues early, reducing the likelihood of costly emergency repairs.
- Reduced Utility Bills: A well-maintained ice machine operates more efficiently, consuming less energy and water. Clogged filters, scale buildup, or malfunctioning components can cause the machine to work harder than necessary, leading to higher utility bills. Regular maintenance keeps the machine running at peak efficiency, saving money in the long run.
7. Choosing the Right Repair Service
Selecting the right repair service for your ice machine is a critical decision that can affect the reliability, efficiency, and longevity of your equipment. With so many options available, it’s essential to know what to look for in a service provider to ensure that you’re entrusting your equipment to qualified professionals who can deliver quality results. When selecting a repair service, consider the following:
- Experience: Look for technicians certified in your machine’s brand.
- Availability: Ensure the company offers emergency services for urgent situations.
- Reputation: Read reviews and ask for references.
Conclusion: Ice Machine Reliability Means Business Success
An ice machine is more than just equipment; it’s a critical asset that impacts your operations, customer satisfaction, and reputation. When it functions properly, it ensures smooth service, fresh food, and happy customers. However, when it breaks down, the consequences can be significant, leading to operational disruptions, financial losses, and customer dissatisfaction.
Timely ice machine repairs prevent these issues, helping you avoid costly downtime and maintain consistent service. By addressing small issues before they escalate, you protect your business from unnecessary expenses and long-term damage. A reliable ice machine enhances your reputation, builds customer loyalty, and supports the efficiency of your operations.
Investing in regular maintenance and professional repairs extends the lifespan of your machine, reduces energy costs, and ensures your business can continue to run smoothly. In the end, a well-maintained ice machine is more than a convenience—it’s a key factor in your business’s long-term success and reliability. Staying proactive ensures that your operations remain cool and your customers stay happy.